SMED - It's not about the name
- Tom Pitlanish
- Sep 18, 2023
- 2 min read
Updated: Sep 24, 2024
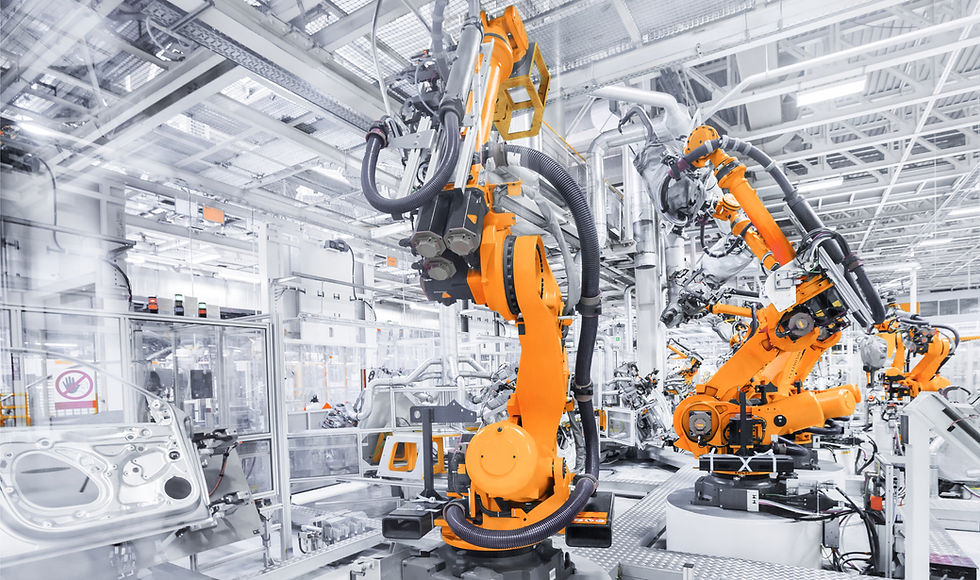
SMED, what’s it all about? SMED is short for Single Minute Exchange of Dies. Developed by Shigeo Shingo in the 1950s (yes, he started this technique in the 50s!) for Toyota. The team was able to reduce changeover time on a 1000 Ton Stamping Press from 4 hours to eventually 3 minutes! It’s not complicated, and it can be easy to implement. Ironically, pushback when implementing is usually along the lines of:
“Well, I’ve heard of that, but it’s for stamping dies, we aren’t a stamper”
“That’s from Toyota, right? We aren’t a Toyota plant. It won’t work here”
“We aren’t changing over dies, so it must not be applicable for us”
“That’s from the automotive industry, we don’t do that”
None of those comments are even remotely true. It can be beneficial, when implementing, to not even reference the term SMED to avoid confusion and pushback. Some great substitutes can be:
Rapid Changeover
Quick Changeover
Precision Changeover
Engineered Changeover
Changeover Optimization
But in the end, it’s not about the name. Its about using the theories and tools with a focused improvement on reducing changeover times. The techniques can be used in any industry, on any type of equipment, that has to go “down” to changeover some component of the equipment.
Just a quick refresher on the standard manufacturing metric of Overall Equipment Effectiveness (OEE). OEE has 3 components: Availability, Performance, and Quality. Optimizing your changeover can have an impact on all three components:
Availability: Measure of Downtime. Reducing your Changeover times can reduce your downtime.
Performance: Slowing a line down due to changeover issues can be eliminated.
Quality: Standardizing changeover can reduce the number of scrap parts to get the first good part during a changeover event.
The other benefits of SMED include the ability to be more flexible in your manufacturing schedule and reduce your end item inventory levels.
The key measurement of changeover is the time it takes to complete the changeover. But when do we start the clock? When do we end the clock? The clock starts when the last good part is produced and the clock ends when the first good part is produced after the changeover event. That should be the time leadership focuses on. Now in some cases, different components of that time can be further delineated (maybe different groups are involved and they want to know how they are performing for the period they are responsible for). In the end though, think “from making money to making money”.
Changeover can have a significant impact on most plant Key Performance Indicators and is usually something that can be implemented in a relatively short period of time allowing for a “quick win” on the shop floor.
Please contact us if you would like to further discuss how optimizing changeover times can impact your business. Remember, the tools and techniques can be used in any industry on any equipment that needs to be “down” to change a component.
Comments